Electronic control systems
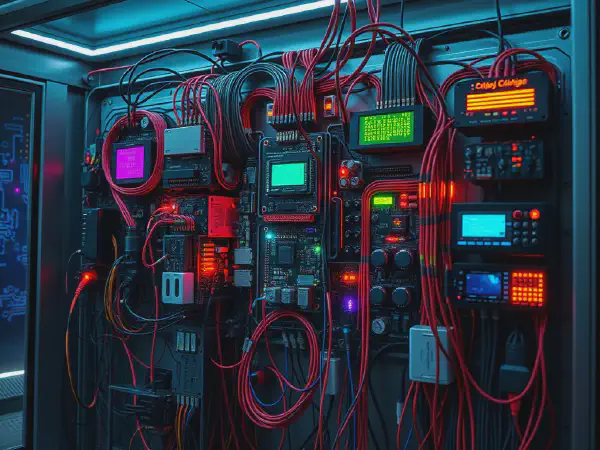
Electronic Control Systems
Understanding Electronic Control Systems in the Automotive Industry
The Significance of Electronic Control Systems
In the modern automotive landscape, Electronic Control Systems (ECS) play a crucial role in enhancing the performance, safety, and efficiency of vehicles. These systems are embedded within vehicles to manage a range of operations including engine performance, transmission effectiveness, and overall vehicle dynamics. The reliance on ECS has dramatically increased as vehicles have evolved from mechanical to highly sophisticated electronic platforms tailored for improved user experience and functionality.
Overview of Subsystems in ECS
Today’s vehicles encompass a multitude of Electronic Control Units (ECUs), each designed to manage specific functions. Some of the key subsystems within electronic control systems include:
- Engine Control Module (ECM): Oversees engine operations, optimizing fuel efficiency and emissions.
- Transmission Control Module (TCM): Manages the transmission system for optimal performance during gear shifts and power transfers.
- Brake Control Module (BCM): Ensures effective braking performance, integrating antilock braking systems and electronic stability control.
- Body Control Module (BCM): Manages various body functions such as lighting, door locking, and climate control systems.
- Suspension Control Module (SCM): Adjusts the vehicle’s suspension settings for ride comfort and handling performance.
The Complexity and Integration of ECUs
The modern vehicle can contain upwards of 150 ECUs, each with a specific role and programmed with increasingly complex embedded software. This integration and complexity present substantial challenges for Original Equipment Manufacturers (OEMs), as they must ensure that these numerous systems communicate effectively, enhancing overall performance and safety while adhering to strict industry regulations.
In the forthcoming sections, we will delve deeper into the intricacies of these subsystems and explore how electronic control systems collectively contribute to automotive innovation and functionality.
What are Electronic Control Systems?
Electronic Control Systems (ECS) are integral components in modern engineering, particularly in automotive applications, where they function as embedded systems responsible for managing various electrical systems and subsystems in vehicles. The core working principle of ECS revolves around the processing of signals—input, process, and output.
-
Input Signals: These are data received from sensors, which detect environmental or operational parameters, converting physical measurements into electrical signals. For instance, a temperature sensor might provide an analogue voltage reading that correlates to the ambient temperature.
-
Process: The core of an ECS is its microcontroller, which interprets input signals and executes the necessary computations or decisions based on pre-defined algorithms. This processing phase is essential for determining how the system responds to the given inputs, often using control algorithms to maintain stability and performance.
-
Output Signals: After processing, output signals are generated. These can drive actuators to perform actions such as adjusting the engine's fuel injection, changing transmission settings, or regulating the braking system. The outputs ultimately influence the vehicle's performance, enhancing safety and efficiency.
Key Components of Electronic Control Systems
Electronic Control Units (ECUs) comprise several critical components that work in unison to facilitate the operation of the ECS. Understanding these components is vital to grasp how ECS operates effectively.
Core Microcontroller
The heart of an ECS is the microcontroller, which executes programmed instructions to control various subsystems. It's responsible for real-time processing and decision-making that allows the ECS to react to dynamic conditions.
Memory Types
- SRAM (Static Random Access Memory): Offers fast access speeds and is often used for temporary data storage during processing.
- EEPROM (Electrically Erasable Programmable Read-Only Memory): Typically used for storing firmware and configuration settings, allowing for data retention even without power.
- Flash Memory: A type of non-volatile storage that can be electrically erased and reprogrammed, commonly used for updates and program storage in ECUs.
Inputs/Outputs
- Inputs: Include supply voltage, ground connections, digital and analog inputs from sensors.
- Outputs: Generally consist of actuator drivers that control physical components like injectors and valves, as well as logic outputs that communicate with other systems.
Communication Links
Effective communication within ECUs is critical for synchronizing operations across various systems. Common communication interfaces include:
- K-Line: A single-wire connection used for diagnostic communication.
- CAN (Controller Area Network): Widely used in automotive applications for real-time data exchange between ECUs.
- Ethernet: Emerging as a high-speed communication standard for modern automotive systems.
Types of Electronic Control Systems
Electronic Control Systems can be categorized based on the nature of their signals. Understanding these distinctions is crucial for applications in automotive engineering.
Continuous-Time Systems
Continuous-time systems handle signals defined across a continuous spectrum. These systems produce an analog signal that varies smoothly over time. A prime example in automotive applications is the engine control system, which continuously monitors parameters like temperature and pressure to adjust fuel delivery in real-time.
Discrete-Time Systems
In contrast, discrete-time systems operate on signals sampled at specific intervals. An example from automotive applications includes digital speed sensors that take readings at set time points, translating these into a digital signal for processing. Discrete-time systems are particularly important in scenarios that require data sampling, such as signal processing and sensor data analysis.
Examples from Automotive Applications
-
Continuous-Time Example: The anti-lock braking system (ABS) continually receives input from wheel speed sensors to modulate brake pressure in real-time, preventing wheel lock-up during braking.
-
Discrete-Time Example: Adaptive cruise control systems use discrete measurements of vehicle speed to adjust throttle commands based on the distance detected by radar sensors at specific intervals, ensuring safe following distances without manual input from the driver.
Understanding these various types of ECS helps engineers design systems that can effectively manage the complexities of modern vehicles, ensuring improved control, performance, and safety.
Electronic Control Systems Components | Functionality and Purpose | Additional Information |
---|---|---|
Engine Control Module (ECM) | Manages engine performance and efficiency | Adjusts fuel injection and ignition timing |
Transmission Control Module (TCM) | Controls shifting and transmission performance | Enhances fuel efficiency by optimizing gear shifts |
Brake Control Module (BCM) | Monitors and manages brake functions | Includes anti-lock braking systems (ABS) |
Central Control Module (CCM) | Coordinates data from various ECUs | Critical for overall vehicle stability |
Body Control Module (BCM) | Handles lighting, security and convenience features | Controls power windows, locks, and lighting systems |
Powertrain Control Module (PCM) | Integrates engine and transmission controls | Enhances vehicle dynamics and fuel economy |
Suspension Control Module (SCM) | Manages adaptive suspension systems | Provides comfort and handling by adjusting suspension |
Embedded Software in ECUs | Performs specific tasks in each control unit | Responsible for diagnostics and system updates |
On-board Diagnostics (OBD) | Monitors vehicle performance and detects issues | Aids in vehicle repair by providing fault codes |
Feedback Systems in Electronic Control | Stabilizes and improves system responses | Uses feedback loops for dynamic control adjustments |
Types of Electronic Control Units (ECUs) in Automotive Systems
Engine Control Unit (ECU)
The Engine Control Unit (ECU), often termed the Engine Control Module (ECM), is vital for optimizing engine performance. It regulates the engine's operation by monitoring various parameters such as engine speed, coolant temperature, and air-fuel ratio. Through precise fuel injection control, the ECU ensures optimal combustion, reducing emissions while maximizing power output. Further, it adjusts ignition timing and oversees other essential functions to enhance vehicle efficiency. Its role is crucial as it directly influences the drivability and fuel economy of the vehicle, making it one of the most important ECUs in modern automotive systems.
Transmission Control Module (TCM)
The Transmission Control Module (TCM) is a specialized ECU that manages the vehicle's transmission system. By analyzing data from various sensors, it determines the optimal timing for gear shifts, thereby ensuring smooth transitions between gears. The TCM also plays a crucial role in power distribution, optimizing how torque is delivered to the wheels under different driving conditions. Additionally, it supports performance tuning by adapting shift patterns based on driver behavior, improving acceleration and handling. This adaptability not only enhances driving comfort but also contributes to overall vehicle efficiency.
Brake Control Module (BCM)
The Brake Control Module (BCM) is essential for maintaining vehicle safety through its management of braking systems. It oversees the operation of anti-lock braking systems (ABS), ensuring that wheels do not lock during sudden stops, which enhances vehicle control. The BCM monitors various inputs such as wheel speed and hydraulic pressure to make real-time adjustments, thereby preventing skidding and maintaining user safety. Furthermore, it interfaces with other safety features, such as electronic stability control (ESC), to provide comprehensive control during critical driving situations. Overall, the BCM significantly increases safety by optimizing braking performance in various conditions.
Body Control Module (BCM)
The Body Control Module (BCM) manages a wide array of vehicle functions that contribute to driver comfort and convenience. It oversees systems like lighting, including headlights and turn signals, as well as power windows and door locks. The BCM is responsible for integrating various electronic modules that control interior features such as climate control and infotainment systems. By streamlining these functionalities, the BCM enhances user experience while improving the vehicle's overall efficiency. Moreover, it plays a role in vehicle security, ensuring that only authorized users can access certain features or unlock the vehicle. This multifunctional role makes the BCM a cornerstone of modern automotive design.
Design and Development of Electronic Control Units (ECUs)
Iterative Design Process Following the V-Model
The design and development of Electronic Control Units (ECUs) is a multifaceted endeavor driven by both hardware and software requirements. Following the V-model, this iterative design process serves as a foundational framework for ensuring that ECUs adhere to rigorous safety and compliance standards, such as ISO 26262.
The V-model emphasizes the relationship between development stages and testing phases. As initial requirements are defined, design specifications are established that lead into development and implementation. The left side of the "V" encompasses requirements analysis, system design, architectural design, module design, and coding. Once development is complete, validation and verification are performed during the right side of the "V", including unit testing, integration testing, system testing, and acceptance testing.
Safety is paramount in automotive systems, hence extensive efforts are dedicated to risk analysis and mitigation from the earliest stages. Adhering to ISO 26262, a standard specifically targeting the safety of electrical and electronic systems in vehicles, helps developers identify potential hazards and implement effective control measures. This involves creating safety requirements, performing design reviews, and conducting comprehensive hazard analysis to ensure long-term reliability and functional safety.
As development progresses, a significant focus on continuous feedback and improvement fosters an environment where both software and hardware iteratively evolve. This flexibility allows for quick response to emerging issues or unexpected results during testing phases, ensuring the final product meets stringent performance metrics and user safety expectations.
Comprehensive Testing and Validation Methods
Testing and validation are integral components of the ECU development cycle, ensuring that each unit functions correctly and reliably within the vehicle's overall system. A variety of methodologies are employed to achieve this, emphasizing thoroughness and compliance with industry standards.
Failure Modes and Effects Analysis (FMEA) is a critical part of this process. FMEA systematically evaluates potential failure modes within the ECU design, assessing their impact on safety and performance. By prioritizing risks based on their severity and likelihood, manufacturers can address critical failures early in the design phase, implement appropriate controls, and validate that these controls are effective through rigorous testing.
On-Board Diagnostics (OBD) systems also play a vital role in the testing and validation of ECUs. OBD facilitates real-time monitoring of vehicle performance, enabling the identification of faults and inefficiencies. By collecting diagnostic data from various sensors and systems, OBD allows engineers to track the performance throughout the vehicle's lifecycle and provides critical insights during both development and post-production phases.
In addition to FMEA and OBD, manufacturers engage in extensive hardware-in-the-loop (HIL) testing, which simulates real-world conditions to validate both hardware and software components before full-scale deployment. HIL testing mimics vehicle dynamics and environmental settings, allowing engineers to observe ECU behavior under various scenarios.
Finally, thorough regression testing ensures that new updates or modifications do not negatively impact existing functions. This comprehensive testing regime guarantees that ECUs are not only reliable but also safe and compliant with automotive industry standards, ultimately leading to enhanced vehicle performance and user satisfaction.
Integration of Electronic Control Units (ECUs) in Modern Vehicles
Streamlining Vehicle Functionality
The integration of multiple Electronic Control Units (ECUs) is rapidly transforming automotive design and functionality. Traditionally, each ECU operates independently, managing specific tasks such as engine control, transmission, and safety systems. However, as vehicles become increasingly complex, manufacturers are gravitating towards a more integrated approach. This trend is driven by the need to enhance efficiency, reduce wiring complexity, and achieve seamless communication between systems.
Multiple ECUs can be consolidated into fewer, multifunctional units, significantly reducing the overall number of components in a vehicle. This not only streamlines manufacturing but also simplifies maintenance, as fewer parts mean fewer potential points of failure. Moreover, integrated ECUs can utilize a common software platform, thereby enhancing the reliability and performance of vehicle systems.
Managing Complexity with Centralized Architectures
Centralized architectures, such as the Domain Controller concept, emerge as a popular solution to mitigate the intricacies of managing numerous ECUs. These architectures allow for the aggregation of functions across several control units into a single controller, thereby managing data more efficiently. By centralizing control, manufacturers can implement advanced features such as over-the-air updates and enhanced data processing capabilities, leading to smarter and more adaptable vehicles.
Furthermore, integration supports advancements in vehicle automation and electrification. With fewer ECUs, the weight and power consumption of the vehicle can be reduced, aligning with the automotive industry's commitment to sustainability and efficiency. The trend towards integrated ECUs not only simplifies the design process but also paves the way for innovative vehicle features, such as advanced driver-assistance systems (ADAS) and electrification that demand high levels of interaction between various vehicle subsystems.
Challenges in ECU Development
Rising ECU Count and Software Complexity
As the number of ECUs in vehicles continues to climb—some modern cars housing as many as 150 distinct units—manufacturers face unprecedented challenges. The escalation in ECU count directly correlates with two significant issues: increased software complexity and heightened development costs. Each additional ECU requires its own software, increasing the time needed for development, testing, and integration. This leads to delays in bringing products to market and can inflate costs associated with recalls or software updates.
Moreover, managing the software lifecycle for numerous ECUs demands sophisticated solutions to prevent inconsistencies and errors. Without a unified approach to software architecture, vehicle manufacturers risk compromised system functionality and increased likelihood of software bugs. OEMs must invest in advanced software frameworks and practices to streamline development, which can divert resources from other essential areas of innovation.
Navigating Safety Standards
In addition to managing rising ECU counts and software intricacies, original equipment manufacturers (OEMs) must adhere to stringent safety standards such as ISO 26262. The complexity introduced by multiple ECUs means that ensuring safety across all vehicle systems becomes increasingly challenging. Each ECU not only needs to operate correctly in isolation but must also interact safely with other units.
This necessitates comprehensive testing strategies, often requiring simulation and validation processes that can be resource-intensive. OEMs are called to adopt robust safety lifecycle processes that account for the entire development cycle of ECUs—right from design to deployment. As vehicle technology evolves, staying compliant with safety standards while managing complexity presents continuous challenges that require strategic foresight and industry collaboration.
Innovations in Electronic Control Systems
Evolution of Electronic Control Units (ECUs)
The future of Electronic Control Systems (ECS) is poised for remarkable advancements as the automotive industry integrates more sophisticated technology. The proliferation of ECUs in modern vehicles, with some models featuring up to 150 control units, demands a paradigm shift towards enhanced communication and processing capabilities. Next-generation ECUs will likely adopt more robust architectures, enabling them to manage increasing complexities and improve inter-module communication.
Integration of Artificial Intelligence
AI-Powered Decision Making
The integration of Artificial Intelligence (AI) into ECS can revolutionize vehicle functionalities. By leveraging machine learning algorithms, vehicles can learn from driver behaviors and environmental conditions to optimize performance dynamically. AI could facilitate predictive maintenance, diagnose potential issues before they arise, and enhance overall vehicle safety by analyzing real-time data to make informed decisions.
Enhanced Data Processing
Future ECS will utilize AI to process vast amounts of data from multiple sensors in real-time, allowing for advanced analytics and more accurate control responses. This capability can lead to improved fuel efficiency, better steering responses, and enhanced adaptive cruise control systems.
Progress Towards Full Autonomy
Autonomous Navigation Systems
The push towards fully autonomous vehicles is significantly influenced by advancements in ECS. These systems will be tasked with interpreting complex sensor inputs from LiDAR, radar, and cameras to create a comprehensive understanding of the vehicle’s surroundings. Innovative algorithms will facilitate seamless integration of path planning and obstacle avoidance, enabling safer navigation in diverse conditions.
Vehicle-to-Everything (V2X) Communication
A cornerstone of future autonomous driving relies on Vehicle-to-Everything (V2X) communication systems. These technologies will enable vehicles to communicate with each other and the infrastructure, improving situational awareness and traffic management. ECS will evolve to include V2X capabilities, promoting safer roadways through coordinated actions between vehicles.
Smart Systems and Connectivity
IoT Integration in Automotive Systems
Smart Systems are becoming integral to the development of future ECS. The Internet of Things (IoT) will enhance connectivity among ECUs, allowing for more efficient data exchange and control. Smart ecosystems can lead to real-time updates and over-the-air (OTA) software patches, ensuring that vehicles remain operationally optimal and secure against cyber threats.
User-Centric Interfaces
Future ECS will prioritize user experience through intuitive interfaces and personalized interactions. The integration of advanced voice recognition systems and gesture controls will allow for more natural commands, enhancing driver interaction with the vehicle’s systems. Predictive analytics will further tailor features to individual preferences, making driving more enjoyable and personalized.
Key Innovations in Automotive Control Systems
Evolution of Electronic Control Units (ECUs)
The emergence of electronic control units (ECUs) has revolutionized vehicle functionality, allowing for the integration of multiple systems such as engine management, transmission controls, and safety features. Modern vehicles may contain upwards of 150 ECUs, reflecting the growing complexity and sophistication of automotive technology. This evolution highlights the critical role that ECUs play in the performance and safety of vehicles.
Increasing Complexity and Challenges
As automotive technology advances, the complexity and interconnectivity of ECUs present significant challenges for original equipment manufacturers (OEMs). Managing the interactions between these systems requires coordinated development efforts to ensure reliability and safety. The industry is increasingly turning to standards such as ISO 26262 to guide the development of safety-critical ECUs, emphasizing the importance of rigorous testing and validation throughout the design process.
Communication and Interconnectivity
Modern vehicles rely heavily on robust communication networks to facilitate the interaction between multiple ECUs. Technologies such as Controller Area Network (CAN) and Ethernet enable seamless data exchange, enhancing system integration and operational efficiency. This interconnectedness not only optimizes vehicle performance but also provides essential data for diagnostics and maintenance, further underscoring the relevance of advanced electronic control systems.
Safety and Reliability in Design
Safety remains a paramount concern in automotive control systems. Manufacturers conduct thorough Failure Mode and Effects Analysis (FMEA) and testing to identify potential risks associated with ECU failures. By adhering to stringent testing protocols, OEMs can develop more reliable and safe vehicles that meet the increasing expectations of consumers and regulatory bodies alike.
Ongoing Relevance of ECUs
The importance of ECUs in the automotive sector cannot be overstated. As the industry continues to embrace innovations such as autonomous driving, electric vehicles, and enhanced connectivity, the role of electronic control systems will only grow. Ongoing advancements in ECU technology will play a pivotal role in shaping the future of mobility, ensuring vehicles are not only more efficient but also smarter and safer.
In summary, electronic control units are integral to modern automotive technology, driving innovations that enhance vehicle performance, safety, and sustainability. Their ongoing development and integration into every aspect of vehicle design remain crucial as the automotive landscape continues to evolve.