HMI panels for industrial automation
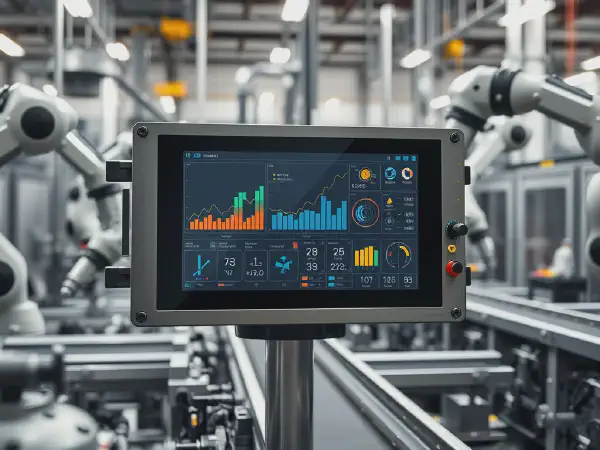
Hmi Panels For Industrial Automation
Understanding HMI Panels in Industrial Automation
What are HMI Panels?
HMI (Human Machine Interface) panels are vital components in modern industrial automation, acting as the bridge between operators and machinery. These interface devices offer graphical or textual displays that represent real-time system data, enabling users to monitor and interact with equipment efficiently. Unlike traditional control panels with simple buttons and switches, HMI panels provide a dynamic and intuitive approach to process management, displaying critical information such as temperature, pressure, and operational status in a user-friendly format. By facilitating seamless communication between the user and machinery, HMI panels play a crucial role in improving operational efficiency and control in various industrial applications.
The Importance of HMI in Industrial Settings
HMI panels significantly enhance operational efficiency and safety within industrial environments. Their ability to visualize complex data in real-time allows operators to make informed decisions quickly, leading to improved process optimization and reduced downtime. Furthermore, advanced features such as alarm notifications, logging capabilities, and remote access provide operators with the tools necessary for proactive monitoring and troubleshooting. This level of oversight not only helps in minimizing operational errors but also contributes to a safer working environment by allowing for timely interventions when anomalies arise. As industry standards evolve, the integration of HMI technology continues to be integral to achieving higher productivity and safety levels in industrial operations.
Exploring Various Types of HMI Panels
Touch Panels: Innovating Interaction
Touch panels stand at the forefront of Human Machine Interfaces (HMIs). Featuring intuitive touchscreen technology, they allow operators to interact with machinery through simple gestures—tapping, swiping, and pinching. Among the various types, capacitive and resistive touch panels are most common. Capacitive panels, known for their sensitivity and multi-touch capability, are widely used in environments requiring precision, while resistive panels offer durability and are often found in harsh industrial applications.
Touch panels are equipped with numerous features, including built-in software drivers that facilitate compatibility with over 40 different manufacturers such as Siemens and Rockwell. Applications range from factory automation to process control, where real-time data visualization and user-friendly interfaces significantly enhance operational efficiency. The integration of advanced graphics and data logging capabilities allows for complex visualizations, making touch panels invaluable in modern industrial settings.
Text and Micro HMIs: Cost-Effective Solutions
For smaller operations or budget-conscious projects, Text and Micro HMIs provide an effective yet economical alternative to full-scale touch panels. These devices typically feature smaller screens and limited graphical capability but excel in displaying critical operational data succinctly.
Micro HMIs usually come with screens up to 6 inches, providing enough real estate for essential text and basic graphics while remaining affordable. They often utilize simple programming interfaces, allowing quick setup and deployment. Their importance in smaller operations cannot be overstated; they serve as a bridge to modern automation without the hefty price tag, enabling businesses to improve their monitoring and control processes affordably.
Remote and Headless HMIs: The Future of Control
The rise of remote and headless HMIs represents a growing trend towards versatile and flexible industrial control solutions. These HMIs operate without a fixed display, allowing data to be transmitted to external monitors via HDMI or other connections. This flexibility lets operators choose a display that best fits their workspace, thus adapting to varying operational environments.
The benefits of remote HMIs are substantial. They allow for centralized control from different locations, which is especially advantageous in large industrial complexes or when monitoring multiple sites. The capability to connect to various devices through established protocols simplifies integration into existing systems. Additionally, headless HRIs often come with enhanced security features, ensuring that sensitive operational data remains protected in an increasingly digital world.
By catering to different operational needs—from high-tech touch screens to cost-effective micro panels and versatile remote interfaces—the selection of HMI panels today plays a crucial role in optimizing automation and control across various industries.
HMI Panels for Industrial Automation | Features and Benefits | Compatibility | Use Cases | Extra Info |
---|---|---|---|---|
HMI ECO Touch Panels | Complimentary Software Available | Built-in drivers for 40+ brands | Flexible communication setup | Plug and Play system for quick connection |
C-more CM5 Series Touch Panels | Large screen sizes (up to 22") with high performance | Supports EtherNet/IP, Modbus | Ideal for high-performance tasks | Embedded SD-card slot for 2TB data storage |
C-more EA9 Series Touch Panels | Graphical interface for easy monitoring and control | Ethernet, USB, serial ports | Suitable for various display needs | Supports numerous screen sizes (up to 15") |
C-more Micro Touch Panels | Affordable panels for budget-conscious applications | Basic PLC communication | Simple text and graphic display | Windows-based setup with built-in simulator |
C-more Headless, Remote HMI | HDMI-enabled for flexible display options | Works with any HDMI display | Remote monitoring applications | USB ports for touch screen compatibility |
ViewMarq Industrial LED Displays | Digital messaging with low power consumption | Configurable via communication | Data communications from PLCs | Supports scrolling messages and multiple lines |
Key Features of Modern HMI Panels
Connectivity Options: Diverse and Flexible Communication
Modern HMI panels offer a variety of connectivity options to support communication with multiple devices and systems. Ethernet connections are increasingly favored for their speed and ability to interconnect networks seamlessly. In addition to Ethernet, USB and serial connections remain critical, providing users with plug-and-play accessibility and the ability to connect directly to personal computers for easy configuration.
Furthermore, these panels support various industrial communication protocols such as Modbus and EtherNet/IP, ensuring compatibility with a wide range of control systems. For instance, many popular HMI models come with built-in drivers for over 40 manufacturers, facilitating quick integration with systems like Siemens LOGO and Rockwell’s MicroLogix. The capacity for multiple simultaneous connections, including the option to toggle between master and slave modes with just a click, enhances the versatility of these systems in diverse industrial environments.
User Interface and Customization: Driving User Engagement
A user-friendly interface is essential in modern HMI panels, as it directly affects operator efficiency and safety. Today's devices prioritize intuitive designs that can display complex data in a straightforward manner, making it easier for users to monitor processes without extensive training. Touchscreens are increasingly common, allowing operators to interact with the systems through familiar gestures, enhancing engagement.
Customization capabilities further empower users to tailor the interface according to specific operational needs. For example, systems like the C-more series HMI panels allow users to create personalized graphical displays, integrating vital information and animations to facilitate real-time monitoring. The ability to configure screens to suit unique operational requirements not only streamlines workflows but also improves overall satisfaction for end-users, reinforcing the importance of a responsive and adaptable design.
Data Communication and Management: Insights Through Analytics
Data communication and management features in modern HMI panels play a crucial role in industrial analytics and monitoring. These systems enable operators to not only receive real-time data but also leverage that information for insights into operational efficiency. With built-in logging capabilities, many panels can capture crucial data points over time, allowing for thorough analysis and reporting.
Advanced functionalities, such as support for secure MQTT protocols and direct connectivity to cloud applications, prepare HMI panels for the IIoT landscape, enhancing their capability in data management tasks. For example, the C-more CM5 series supports the secure transfer of information across networks, ensuring that sensitive data remains protected. Additionally, the ability to share information between separate networks empowers operators to make informed decisions swiftly, adopting proactive approaches to system management.
Overall, these features facilitate robust monitoring solutions and foster a proactive culture around data utilization within industrial environments.
Choosing the Right HMI Panel
Assessing Your Operational Requirements
When selecting an HMI panel, it's essential to first assess your operational needs. Consider the size of the interface; larger screens can display more information but may require more space and budget. Evaluate connectivity options as well—ensure the panel can integrate seamlessly with your existing control systems, whether they involve PLCs or industrial PCs. Moreover, budget constraints are a significant factor. Determine what features are critical for your operations and seek out HMIs that offer the best balance between cost and functionality.
Evaluating HMI Performance Parameters
Performance is crucial when investing in an HMI panel. Look for key specifications such as processing speed, memory capacity, and supported communication protocols. High-speed processors facilitate smoother operations, while sufficient memory ensures the HMI can handle complex applications and graphics. Additionally, compatibility with various communication standards, like Modbus or EtherNet/IP, is vital for ensuring seamless integration with your equipment and systems. Make sure to review performance benchmarks to understand how different models stack up against one another in real-world applications.
Key Vendor Considerations for HMI Selection
Choosing the right vendor can be just as important as the HMI panel itself. Start by researching manufacturer reputation—look for established companies known for reliability and excellent customer support. It's also essential to consider the range of products they offer; a vendor with extensive options might better serve your evolving needs. Evaluate warranty terms, service agreements, and availability of software updates for the HMI panels. Additionally, consider whether the vendor provides complimentary software and drivers to facilitate easy setup and integration—this can save valuable time during installation.
Real-world Applications of HMI Panels
Optimizing Manufacturing Processes with HMI Panels
In manufacturing settings, Human Machine Interface (HMI) panels play a crucial role in optimizing productivity. For instance, in automotive assembly lines, HMI panels are utilized to monitor and control operational parameters such as machine speed, temperature, and material flow. Systems like Siemens LOGO and Rockwell Compact are commonly integrated into these panels, allowing real-time data collection and analysis. This enables operators to identify potential bottlenecks quickly and adjust processes accordingly.
Additionally, industries implementing HMI solutions often utilize built-in software drivers that support more than 40 different manufacturers, significantly enhancing the flexibility and scalability of their automation systems. The ability to toggle between master and slave modes quickly can streamline operations, further optimizing workforce efficiency.
Enhancing Control in Processing Industries
In processing industries such as food manufacturing and chemical production, HMIs facilitate precise control and monitor intricate processes. For example, in food production, HMI panels manage temperature and humidity controls to ensure products meet safety regulations. These systems also track batch records through data logging features, ensuring compliance and traceability.
In the chemical sector, HMI panels help monitor reactants and control various parameters like pressure and pH levels, which are critical to maintaining product quality. With real-time alerts and historical data analysis capabilities built into many HMI panels, operators can promptly address issues, reducing downtime and enhancing overall production efficiency.
Innovative Custom Applications for Specialized Industries
HMI panels are not limited to traditional applications, as they can be tailored for specialized industries, resulting in innovative solutions. For example, in the renewable energy sector, HMI panels are employed to monitor solar panel arrays and wind turbines. These panels can interface with different monitoring systems to provide a comprehensive overview of energy production and equipment status, optimizing maintenance schedules.
Moreover, sectors like pharmaceuticals use custom HMI solutions for critical operations such as cleanroom monitoring. These HMIs display essential parameters like airborne particle count and temperature, enabling compliance with stringent industry standards. The adaptability of HMI panels opens doors for further innovation, ensuring that organizations in specialized fields can harness the power of automation and improve operational efficiencies.
Future Trends in HMI Technology
Integration with the Industrial Internet of Things (IIoT)
The evolution of Human-Machine Interfaces (HMIs) is increasingly influenced by the rise of the Industrial Internet of Things (IIoT). This integration transforms traditional HMI panels into sophisticated systems capable of real-time data exchange and remote monitoring. With IIoT, HMIs can connect to a vast network of sensors and devices, enabling seamless communication across the manufacturing floor. These advancements facilitate enhanced operational efficiency, predictive maintenance, and reduced downtime by allowing operators to visualize system performance and receive alerts for anomalies instantly.
HMIs equipped with IIoT capabilities can aggregate data from various sources, providing actionable insights directly on the user interface. Moreover, the ability to log and analyze historical data can lead to improved decision-making and faster response times to changing production requirements. As more manufacturers recognize the value of IIoT integration, HMIs will become critical for managing complex industrial environments, ultimately driving productivity and innovation across sectors.
Advanced Analytics and Artificial Intelligence in HMIs
The future of HMI technology is also poised to embrace advanced analytics and artificial intelligence (AI), resulting in smarter and more intuitive operations. AI-enabled HMIs can analyze vast amounts of data in real-time, identifying patterns and anomalies that human operators might overlook. This capability empowers industries to optimize processes, enhance user interactions, and streamline workflows.
As AI algorithms are integrated into HMIs, users will benefit from features like predictive analytics, which can forecast potential machine failures and suggest preventive actions. Additionally, natural language processing (NLP) will enable intuitive interactions between operators and machines, allowing users to communicate using everyday language rather than technical jargon.
The incorporation of such analytics will enhance decision-making capabilities, helping operators understand complex data through visualizations, alerts, and recommendations, ultimately fostering an environment of continuous improvement and innovation. As these technologies advance, HMIs will evolve from mere user interfaces into powerful tools that not only monitor but also optimize manufacturing processes in real-time.
FAQs about HMI Panels for Industrial Automation
Common Questions Regarding HMI Integration
- What is an HMI Panel and its primary function in industrial automation?
-
HMIs (Human Machine Interfaces) display graphical or textual representations of system conditions to facilitate process monitoring and control.
-
How do I connect an HMI to my PLC or control system?
-
Most HMI panels include built-in software drivers for common manufacturers like Siemens and Rockwell, enabling plug-and-play connections.
-
Can I use multiple HMI panels in a single application?
-
Yes, many HMI systems allow for multiple parallel connections, which can enhance operation efficiency.
-
What communication protocols are commonly supported by HMI panels?
-
HMIs typically support protocols like EtherNet/IP, Modbus, and MQTT, providing flexibility for various industrial applications.
-
How do I troubleshoot connectivity issues with my HMI?
- Check the compatibility of the HMI with your control system, ensure the correct drivers are installed, and verify network configurations.
Technical Support and Resources for HMIs
- Manufacturer Support Websites:
-
Each HMI manufacturer often provides robust technical support resources on their website, including FAQs, troubleshooting guides, and software downloads.
-
Online Forums and Communities:
-
Platforms like AutomationDirect offer customer forums where users can share experiences and solutions related to HMI applications.
-
Training and Webinars:
-
Many manufacturers provide online training sessions and webinars, covering HMI integration, programming, and best practices for usage.
-
Documentation and Manuals:
-
Comprehensive user manuals and installation guides are typically available for download, offering detailed setup instructions and operational advice.
-
Contacting Sales or Technical Support:
- Fill out a contact form on the manufacturer’s website for personalized assistance or to request product information tailored to your needs.