Industrial electronic repair services
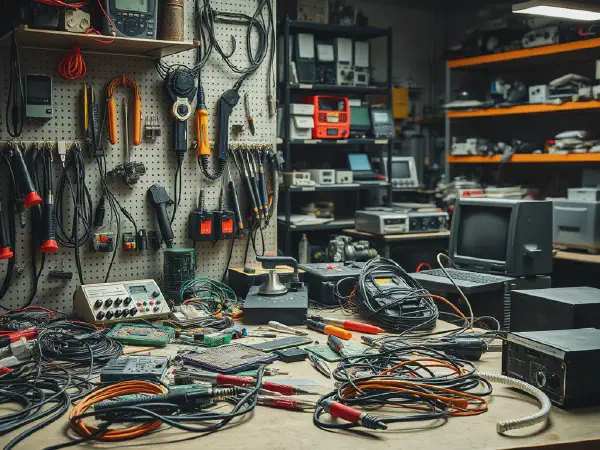
Industrial Electronic Repair Services
Overview of Industrial Electronic Repair Services
Definition and Importance of Industrial Electronic Repair Services
Industrial electronic repair services encompass a wide range of technical activities focused on diagnosing, repairing, and maintaining electronic equipment used in various industrial settings. This includes everything from control systems and robotics to power supplies and automation devices. The significance of these services cannot be overstated, as they play a crucial role in minimizing downtime, enhancing operational efficiency, and extending the lifecycle of expensive equipment. Having reliable repair services ensures that manufacturers can maintain productivity and avoid the high costs associated with equipment failure, making these services indispensable in today's fast-paced industrial environment.
Common Applications of Industrial Electronic Repair Services Across Industries
Industrial electronic repair services are utilized in a variety of sectors, each with unique applications. In manufacturing, for instance, automation controllers and programmable logic controllers (PLCs) are vital for streamlined production processes, necessitating regular maintenance and repair. Similarly, the energy sector relies on intricate electronic systems for monitoring and control, requiring prompt repair services to maintain grid stability. Additionally, the automotive industry employs a range of sophisticated electronics in manufacturing and repair processes, further highlighting the need for specialized repair services. Other applications extend to food processing, aerospace, and pharmaceuticals, where precision and reliability are paramount. This broad applicability underscores the crucial role these services play in supporting the infrastructure of various industries.
Types of Industrial Electronic Repairs
Repair of Industrial Circuit Boards
Industrial circuit boards are crucial components in various machinery and electronic devices, responsible for controlling processes and ensuring efficient operation. The repair of circuit boards often involves diagnosing issues such as burnt traces, faulty components, or damaged solder joints. Skilled technicians utilize specialized tools like oscilloscopes and multimeters to accurately identify faults. Once the problem is pinpointed, they can replace defective components, reflow solder, or repair traces using conductive paints or wires. This meticulous process not only reinstates the functionality of the circuit board but also extends its lifespan, ultimately saving businesses significant costs compared to full replacements.
Repairing Power Supplies
Power supplies are the backbone of industrial electronic systems, providing the necessary voltage and current for optimal operation. When these units fail, it can lead to widespread downtime. Repairing power supplies involves a thorough examination to detect common issues such as blown fuses, damaged transformers, or faulty capacitors. Technicians often start by checking input and output voltages to gauge functionality. After identifying the faulty parts, they replace or repair the damaged components, ensuring that the power supply operates within specified parameters. Timely repair of power supplies is crucial to maintain system stability and efficiency in industrial environments.
Repair of Control Systems
Control systems are integral to automating and managing industrial processes. When these systems experience malfunctions, it can disrupt workflows and productivity. The repair of control systems requires a comprehensive understanding of both hardware and software components. Technicians begin by inspecting wiring, connectivity, and the functionality of sensors and actuators. They may also analyze the control software to identify glitches or bugs. By addressing both the physical and digital aspects of control systems, technicians can restore full operational capacity, minimizing disruptions and enhancing the overall efficiency of industrial operations.
Industrial Electronic Repair Services | Benefits of Choosing Expert Repair Services | Common Issues in Industrial Electronics | Repair Process Overview | Cost Factors for Repair Services |
---|---|---|---|---|
Comprehensive diagnostics and repairs | Quick turnaround time | Equipment failure | Initial assessment | Parts required for repair |
Substantial experience in the field | Extended equipment lifespan | Signal disruptions | Troubleshooting | Labor costs, hourly rates |
Use of quality replacement parts | Cost-effective solutions | Power supply issues | Repair confirmation | Location of the facility |
Skilled technicians with certifications | Increased efficiency of machinery | Short circuit problems | Ongoing support | Type of electronic equipment being repaired |
Warranty on repair services | Enhanced safety and compliance | Communication breakdowns | Final testing | Age and condition of the equipment being repaired |
The Repair Process
Initial Diagnostics
The first step in the repair process is conducting thorough diagnostics. This involves assessing the device or system to identify the root cause of the issue. Technicians often use specialized tools and diagnostic software to pinpoint problems, making it easier to determine the necessary repairs. It is essential to gather customer complaints and observe symptoms firsthand, as this can provide valuable insight. Documenting the issues carefully leads to a more structured approach in subsequent stages and ensures that no aspect of the diagnosis is overlooked. Accurate initial diagnostics are crucial, as they lay the groundwork for successful repairs.
Component Testing
Once initial diagnostics have been completed, component testing takes center stage. This phase involves systematically checking each part of the device to verify its functionality. Technicians will often use multimeters, oscilloscopes, or other testing instruments to measure electrical signals, resistance, and voltages. Focusing on the most likely components to fail—such as power supplies, circuit boards, or batteries—can lead to quicker resolutions. Testing should be thorough but efficient, allowing for a balance between time management and accuracy. The data collected during component testing not only helps in pinpointing issues but also serves as a reference for future repairs.
Repair Techniques and Best Practices
Having identified the problematic components through diagnostics and testing, technicians now employ various repair techniques and best practices. Soldering, replacing parts, or reprogramming firmware are common methods utilized, depending on the nature of the issue. Technicians should adhere to safety protocols to minimize the risk of further damage or injury during repairs. Additionally, utilizing high-quality replacement parts is essential to ensure longevity and reliability. Documenting each step taken during the repair process will provide a comprehensive history for future reference. Effective communication with clients about the repair process, expected outcomes, and potential follow-ups is also critical. Employing these best practices not only enhances the quality of repairs but also boosts customer satisfaction.
Selecting the Ideal Repair Service for Your Needs
Key Considerations for Choosing a Repair Service
When choosing a repair service, several essential factors can determine the quality and reliability of the service you receive. First, consider the service provider’s experience and expertise in your specific type of repair. Longer-operating companies often have a proven track record and comprehensive knowledge of the necessary repair techniques.
Next, evaluate the service provider's certifications and licenses. These credentials ensure that the technicians are properly trained and adhere to industry standards, which is crucial for guaranteeing quality work. Additionally, assess their warranty and guarantee policies; a reputable service provider should stand behind their work and offer assurance in case of future issues.
Cost is another important factor. While you don’t want to compromise on quality, obtaining quotes from different providers can help you gauge the market rate. Beware of significantly lower prices that may indicate subpar service or hidden fees.
Lastly, consider customer reviews and references. Insights from previous clients can provide a clearer picture of the service quality and customer satisfaction levels. Platforms like Google, Yelp, and trusted trade organizations can offer valuable feedback and ratings to help inform your decision.
Essential Questions to Ask Your Potential Repair Provider
Before committing to a repair service, it’s crucial to ask the right questions to ensure you make an informed decision. Start with inquiries about the provider’s experience. For instance, "How long have you been specializing in this type of repair?" This will give you an idea of their expertise in specific areas.
Next, ask about the technicians who will be handling your repair. Questions like, "Are your technicians certified and insured?" can help you assess their qualifications and assurance of protection against any potential damages or accidents during the repair process.
Inquire about their approach to pricing. "Do you provide a written estimate before starting the work?" is crucial, as it helps avoid unexpected costs down the line. Clarifying warranty policies is also important; ask, "What warranty do you offer on repairs?" to ensure you are covered should any issues arise post-service.
Lastly, gauge their responsiveness and professionalism with questions like, "How quickly do you typically respond to service requests?" A reliable company should prioritize customer communication and service responsiveness.
Taking the time to evaluate these factors and ask pertinent questions will lead you to the best repair service that meets your needs efficiently and effectively.
Preventative Maintenance and Support
The Critical Role of Regular Maintenance
Regular maintenance is essential for ensuring the longevity and efficiency of equipment and systems. It not only minimizes the risk of unexpected breakdowns but also helps identify potential issues before they escalate into significant problems. By investing time and resources into regular maintenance, organizations can protect their assets, improve safety, and reduce overall costs associated with repairs and replacements.
Preventative maintenance can also enhance operational efficiency. Equipment that is well-maintained operates more smoothly and effectively, leading to higher productivity levels. Additionally, regular checks and servicing allow for the optimization of performance parameters, ensuring that systems run at peak efficiency. Overall, prioritizing regular maintenance is a smart strategy that pays off in numerous ways, from financial savings to improved reliability.
Effective Strategies for Maintenance Programs
To implement an effective maintenance program, organizations should adopt a structured approach that includes comprehensive planning and execution. Firstly, developing a maintenance schedule that outlines specific tasks and their frequency can streamline the process and ensure no critical activities are overlooked. This schedule should be tailored to the unique needs of your equipment and systems, taking into account manufacturers' recommendations and industry standards.
Secondly, documenting all maintenance activities is crucial for tracking performance and identifying trends. This data can be used to continually refine maintenance practices, optimizing costs and enhancing equipment reliability.
Furthermore, organizations should consider utilizing technology to improve their maintenance programs. Software solutions that monitor equipment performance in real-time can provide invaluable insights, allowing for timely interventions and reducing the risk of equipment failure. Implementing a combination of these strategies can significantly enhance the effectiveness of maintenance programs, ensuring a proactive rather than reactive approach.
Identifying When to Seek Professional Assistance
Even with the best-maintained systems, there are times when professional help is necessary. Organizations should be vigilant in recognizing the signs that indicate a need for expert intervention. Unusual noises, decreased performance, or frequent breakdowns can all signal underlying issues that require specialized knowledge and tools to address effectively.
Furthermore, during periods of significant equipment use or after major incidents, it may be prudent to consult professionals to ensure that all maintenance requirements are met. Engaging experts not only brings a wealth of experience but also the benefit of specialized equipment and techniques that may not be available in-house.
Finally, organizations should keep in mind that while regular maintenance can mitigate many common issues, certain repairs or assessments—such as those involving complex systems or safety equipment—should always be left to professionals. Knowing when to seek professional help can save time, money, and ultimately, enhance safety and operational efficiency.
Cost Considerations in Repair Services
Analyzing Pricing Structures and Estimates
When seeking repair services, understanding the pricing structures is crucial for making well-informed decisions. Many companies employ various pricing models, including flat rates, hourly rates, or a combination of both. Flat rates offer transparency as they provide a fixed price for specific services, making it easier for customers to budget accordingly. On the other hand, hourly rates might initially seem lower, but they can lead to unexpected costs if the repair takes longer than anticipated.
Before committing to a service provider, it's advisable to request detailed estimates. A comprehensive estimate should break down the costs of labor, parts, and any additional fees. This clarity helps customers compare prices among different providers and ensures there are no hidden charges. It's also beneficial for customers to inquire about any potential additional expenses that may arise during the repair process. Understanding the full scope of potential costs upfront is essential to avoid any surprises when the final bill arrives.
Grasping Warranty and Service Guarantees
Warranties and service guarantees can significantly impact the overall cost and satisfaction of repair services. A strong warranty indicates that the service provider stands behind their work and is willing to address any issues that may arise after the repair is completed. Customers should always inquire about the specific terms of the warranty, including its duration and what it covers. It's common for good companies to offer warranties on both parts and labor, which provides further peace of mind.
In addition to warranties, service guarantees can be a key factor in choosing a repair provider. A service guarantee often assures customers that if the repair does not meet certain standards or if the same issue recurs shortly after the service, the provider will rectify the problem at no extra cost. Customers should clarify the details of these guarantees, including the time frame and any conditions that may apply. Understanding these elements helps customers feel confident in their choice and can ultimately save money in the long run by avoiding potential repeat repairs.
Future Trends in Industrial Electronics Repair
Innovations in Repair Technologies
The landscape of industrial electronics repair is rapidly evolving, with advancements in repair technologies leading the charge. Techniques such as robotic-assisted repairs, which automate the disassembly and reassembly processes, are becoming commonplace. Furthermore, the utilization of augmented reality (AR) in diagnostic repair allows technicians to visualize complex systems and access real-time data, enhancing accuracy and efficiency. 3D printing also plays a pivotal role, enabling the production of customized replacement parts on demand, thus reducing lead times significantly. These innovations not only streamline repair processes but also minimize costs associated with traditional manufacturing and procurement. As these technologies mature, the speed and reliability of repairs are anticipated to improve dramatically, setting new standards within the industry.
The Influence of Industry 4.0 on Repair Practices
The advent of Industry 4.0 has a profound impact on industrial electronics repair. By integrating IoT (Internet of Things) devices, companies can monitor equipment in real-time, enabling predictive maintenance that foresees failures before they occur. This proactive approach contrasts sharply with traditional reactive repair methods, ultimately minimizing downtime and enhancing operational efficiency. Additionally, big data analytics empowers businesses to analyze repair trends and performance metrics, allowing for informed decision-making and optimized resource allocation. Machine learning algorithms further refine these insights by predicting the most effective repair strategies. As businesses embrace these innovations, the transformation of repair practices ensures a more resilient and responsive industrial landscape, catering to the demands of modern manufacturing environments.
Frequently Asked Questions (FAQs)
What Types of Industrial Electronics Can Be Repaired?
Industrial electronics encompass a broad range of devices and systems used in manufacturing and production environments. Commonly repaired items include programmable logic controllers (PLCs), variable frequency drives (VFDs), power supplies, control panels, and sensors. Specialized equipment such as CNC machines and industrial robotic systems also fall under this category. Many repair services are equipped to handle various brands and models, ensuring that you get the necessary support for your specific equipment needs.
How Long Does the Average Repair Take?
The duration of repairs can vary significantly based on the type of equipment, the extent of the damage, and the availability of replacement parts. Generally, minor repairs can be completed within a day or two, while more complex issues may take a week or longer. Repair services often provide estimated timeframes upon diagnosis to help you plan your operations accordingly. In urgent situations, many companies also offer expedited services for critical equipment needing immediate attention.
What Are the Signs That My Equipment Needs Repair?
Being proactive about equipment maintenance is crucial for preventing costly downtime. Key indicators that your industrial electronics may need repair include unusual noises, erratic behavior, warning lights, and decreased performance or efficiency. Additionally, if equipment frequently trips or malfunctions, it’s a clear sign that professional evaluation and repair are necessary. Regular inspections and monitoring can help identify these signs early, allowing for timely intervention.
Can I Perform Repairs In-House or Should I Hire a Service?
Deciding whether to handle repairs in-house or hire a professional service depends on several factors, including the complexity of the equipment and your team's expertise. Simple issues may be manageable by trained staff, reducing downtime and costs. However, for advanced repairs, it’s generally advisable to seek professional help. Specialized technicians possess the skills, tools, and experience needed to diagnose and fix complex problems safely and efficiently, ensuring long-term reliability and performance.