Industrial electronic testing equipment
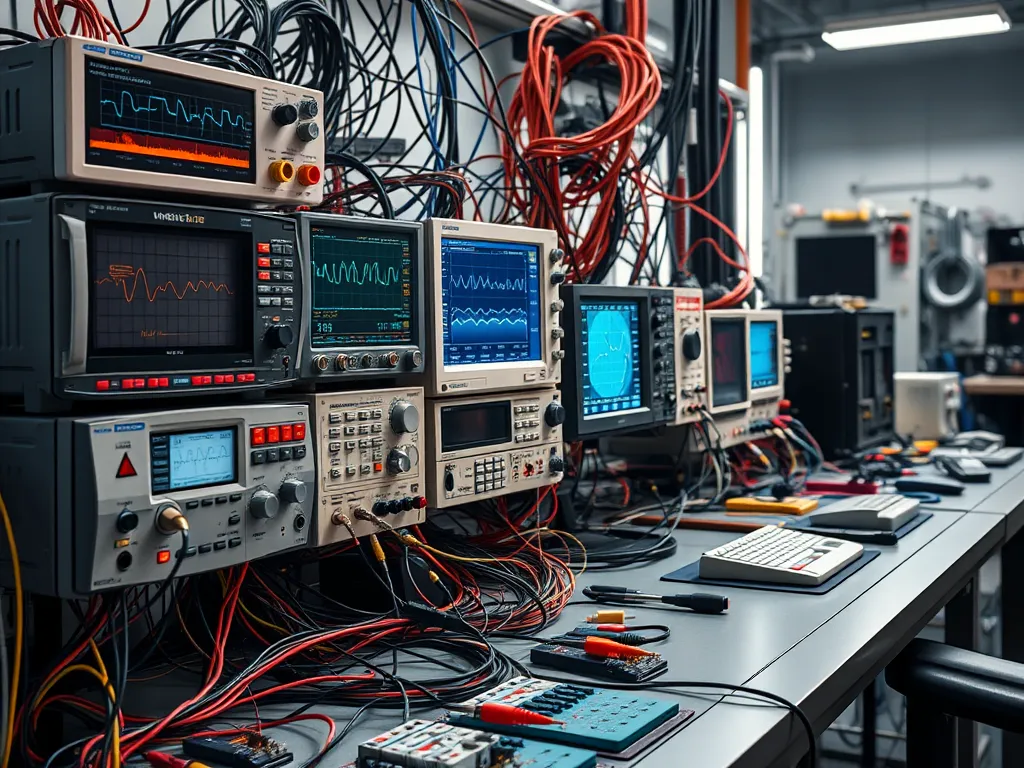
Industrial Electronic Testing Equipment
Understanding Industrial Electronic Testing Equipment
Definition and Significance of Industrial Electronic Testing Equipment
Industrial electronic testing equipment refers to the specialized instruments used to measure, analyze, and evaluate the performance of electronic components and systems within industrial settings. This category includes devices such as multimeters, oscilloscopes, function generators, and spectrum analyzers. These tools are essential for ensuring that electronic systems function correctly, comply with safety standards, and meet industry regulations.
The importance of industrial electronic testing equipment cannot be overstated. It plays a critical role in various industries, including manufacturing, telecommunications, automotive, and aerospace. By identifying issues before they escalate, these tools help in minimizing downtime, improving product quality, and ensuring the reliability of electronic systems. Moreover, they support preventive maintenance efforts, which can lead to significant cost savings and enhanced operational efficiency.
Historical Evolution of Industrial Electronic Testing Equipment
The development of industrial electronic testing equipment has a rich history that dates back to the early 20th century. The invention of the vacuum tube in the 1920s marked a pivotal moment, laying the groundwork for more sophisticated testing devices. Soon after, in the 1930s, the introduction of the oscillograph allowed for the visualization of electrical signals, providing engineers with invaluable insights into circuit behavior.
In the 1960s, the advent of integrated circuits stimulated a further evolution in testing technologies. Digital multimeters emerged, offering enhanced accuracy and versatility compared to their analog counterparts. By the 1980s and 1990s, computer-based test systems began to proliferate, enabling engineers to conduct complex analyses and streamline testing processes.
Today, industrial electronic testing equipment continues to evolve, integrating features like automation, wireless connectivity, and advanced data analytics. These advancements not only enhance measurement accuracy but also streamline workflows, fostering innovation across various industrial sectors. The historical milestones in this field highlight the ongoing significance of testing equipment in maintaining the functionality and reliability of electronic systems in an increasingly complex technological landscape.
Types of Industrial Electronic Testing Equipment
Multimeters: Essential Measurement Tools
Multimeters are versatile instruments used to measure voltage, current, and resistance in electrical components and circuits. Their functionality allows them to operate in different modes, making them indispensable in industrial settings. A standard multimeter can measure direct current (DC) and alternating current (AC), and many models offer additional features like temperature measurement, diode testing, and continuity testing.
In industry, multimeters are utilized for troubleshooting electrical systems, ensuring the accuracy of circuit installations, and performing routine maintenance checks. They are essential for electricians and technicians to ensure that machines operate within specified parameters, thus reducing downtime and preventing equipment failure. Digital multimeters, with their clear displays and enhanced accuracy, have become the standard over traditional analog multimeters.
Oscilloscopes: Visualizing Electrical Signals
Oscilloscopes are powerful diagnostic tools that enable engineers to visualize electrical signals in real-time. By displaying voltage over time on a graph, oscilloscopes help users analyze signal characteristics such as frequency, amplitude, and waveform shape. This capability is crucial for diagnosing issues within electronic devices and circuits.
In industrial applications, oscilloscopes can be used to monitor and debug complex electronics, test the integrity of signal paths, and investigate the behavior of transient signals. They are vital in fields such as telecommunications, automotive, and power distribution, where understanding the waveform of electrical signals is essential for performance optimization and failure analysis.
Function Generators: Creating Test Signals
Function generators are electronic devices that produce various types of waveforms, including sine, square, triangle, and sawtooth waves. Their primary purpose is to simulate different electrical signals for testing and designing electronic circuits. By adjusting frequency, amplitude, and offset, engineers can generate signals tailored to specific testing requirements.
In an industrial context, function generators are used extensively in research and development, manufacturing, and maintenance to test circuits and devices under multiple conditions. For instance, they enable engineers to evaluate a circuit’s response to varying frequency inputs, aiding in the design and refinement of products. Additionally, function generators are utilized in signal integrity testing to ensure systems operate reliably without interference or distortion.
Industrial Electronic Testing Equipment Type | Features | Applications | Specs & Specifications | Extra Info |
---|---|---|---|---|
Oscilloscope | High bandwidth, multiple channels | Circuit analysis, debugging | 100 MHz bandwidth, 1 GS/s sampling rate | Ideal for capturing fast electrical signals. |
Multimeter | Measure voltage, current, resistance | Troubleshooting and repair | 10 mV to 1000 V range, 10A | Essential for accurate electrical measurements. |
Signal Generator | Generates various waveform signals | Testing and development | Frequency range 1 Hz to 100 MHz | Useful for simulating signals in circuits. |
Power Supply Tester | Tests power supply voltage and current | Power supply validation | Output range from 0-30V | Ensures stable operation of electronic devices. |
Function Generator | Produces standard waveforms | Circuit testing | Frequency up to 10 MHz | Enables testing of amplifiers and filters. |
Frequency Counter | Measures frequency of input signals | Signal analysis | Frequency range up to 1 GHz | Necessary for precise frequency measurement. |
Data Logger | Records voltage, current over time | Research and monitoring | Storage capacity up to 1 million samples | Great for long-term data collection. |
Advantages of Using Testing Equipment
Boosting Production Efficiency through Testing Tools
Testing equipment plays a vital role in enhancing efficiency within production processes. By automating testing procedures, manufacturers can significantly reduce the time spent on manual inspections and audits. This acceleration in testing allows for faster production cycles, wherein products can move quickly from development to market with minimal delay. Moreover, advanced testing technologies can detect issues earlier in the production line, reducing downtime and the likelihood of costly rework. When testing procedures become streamlined, teams can focus on scaling operations and improving overall productivity while maintaining high standards.
Ensuring Quality Standards with Testing Equipment
The critical function of testing equipment lies in its ability to uphold quality assurance standards across various products. Regular testing ensures that products meet the necessary specifications and regulations, fostering consumer trust and brand loyalty. Utilizing testing tools that provide precise measurements means manufacturers can identify deviations from quality benchmarks and rectify them before products reach the market. This proactive approach not only mitigates the risk of recalls but also supports continuous improvement processes, as data collected from testing can be analyzed to enhance product design and manufacturing practices.
Optimizing Costs through Effective Testing Solutions
Implementing testing equipment can lead to substantial cost reductions in production and maintenance. By identifying defects early and addressing them in real-time, companies can decrease the amount invested in scrapped materials and rework labor. Furthermore, a reduction in product failures translates to lower warranty costs and fewer customer complaints, ultimately protecting profit margins. The initial investment in advanced testing technologies can be recouped over time, as savings accumulate from improved efficiencies and enhanced product reliability. Overall, testing equipment is not just an operational tool; it is an investment in long-term financial viability.
Challenges and Considerations
The Importance of Calibration and Maintenance for Accuracy
Regular calibration and maintenance of testing equipment are crucial to ensure the accuracy and reliability of test results. Over time, equipment can drift from its calibrated settings, leading to potential errors that may compromise data integrity. Periodic checks and recalibrations help identify any discrepancies, ensuring that the results produced by this equipment adhere to required standards. Moreover, maintaining equipment in optimal condition can extend its lifespan and reduce the likelihood of unexpected failures that could disrupt testing processes.
Failing to calibrate equipment regularly may result in incorrect readings, affecting not only the quality of the testing but also the end products, which can have serious implications, especially in industries like healthcare or manufacturing. Therefore, developing a robust calibration schedule, along with routine maintenance checks, is essential for any organization relying on testing equipment.
Necessity for Training and Expertise
The effectiveness of testing equipment largely depends on the personnel operating it. Trained professionals are essential for the correct usage, troubleshooting, and maintenance of the equipment. It’s not enough to have the right tools; the individuals who work with them must possess the necessary skills and knowledge to ensure optimal performance and compliance with safety regulations.
Investing in ongoing training programs equips staff with up-to-date techniques and informs them about the latest advancements in technology. This emphasis on expertise not only enhances the reliability of test results but also fosters a culture of safety and accountability in the workplace. Properly trained personnel can identify potential issues before they become costly problems, thereby safeguarding both the equipment and the integrity of the testing process.
Addressing Technological Obsolescence
In an era where technology evolves rapidly, testing equipment can become obsolete more quickly than ever. This obsolescence presents challenges as newer models often come with advanced features, improved accuracy, and compliance with updated industry standards. Organizations may face difficulties in justifying investments in newer equipment, particularly if existing tools are still functional, albeit outdated.
However, sticking to outdated technology can lead to inefficiencies, lost competitiveness, and the inability to meet regulatory requirements. To mitigate these risks, organizations should regularly assess their equipment inventory against current industry trends and technology advancements. Developing a clear replacement strategy ensures that the organization remains at the forefront of technological innovation while continuing to produce reliable and accurate testing results.
Innovations Shaping Industrial Electronic Testing
The Role of Automation and AI in Testing Equipment
The integration of automation and artificial intelligence (AI) in industrial electronic testing is revolutionizing the landscape. These technologies are streamlining testing processes, reducing human error, and enhancing precision. Automated systems are capable of performing repetitive tasks with high accuracy, while AI algorithms can analyze vast amounts of data in real-time, identifying anomalies and suggesting corrective actions. As a result, the development of testing equipment is increasingly focused on incorporating these intelligent features, allowing for more efficient test cycles and improved overall quality control. Moreover, as AI continues to evolve, its ability to learn from past test results will further optimize future testing protocols, making the processes smarter and faster.
Breakthrough Technologies on the Horizon
Looking ahead, several emerging technologies are poised to impact industrial electronic testing significantly. Among these, 5G technology stands out, promising faster data transmission and enabling real-time monitoring and testing from remote locations. Additionally, advancements in Internet of Things (IoT) devices will allow for continuous data collection and analysis, providing insights that were previously unattainable. Quantum computing also holds potential for complex calculations and simulations, which could refine testing methodologies. Furthermore, advanced materials such as flexible electronics and nanotechnology may introduce new parameters for testing standards. Collectively, these innovations herald a new era of capabilities, enhancing the reliability and effectiveness of electronic testing in various industries.
Key Takeaways and Final Thoughts
Recap of Essential Insights
In this article, we explored the critical role of industrial electronic testing in ensuring safety and reliability in manufacturing and production processes. We highlighted the importance of maintaining compliance with industry standards and regulations to mitigate risks and enhance product quality. Additionally, we discussed various testing methodologies, including functional, performance, and environmental testing, emphasizing the value of adopting robust testing procedures throughout the product lifecycle.
Empowering Action in Electronic Testing
Now that we've established the significance of industrial electronic testing, we encourage readers to evaluate their own contexts. Consider how implementing structured testing processes can not only safeguard your operations but also elevate product excellence. Engage with industry experts and invest in training to empower your teams with the skills needed to effectively utilize testing technologies. Take steps today to integrate electronic testing as a cornerstone of your compliance and quality assurance efforts, paving the way for innovation and market leadership.
Frequently Asked Questions (FAQs)
Common Types of Electronic Testing Equipment
Electronic testing equipment plays a crucial role in various industries. The most common types include:
- Multimeters: Used to measure voltage, current, and resistance in electrical circuits.
- Oscilloscopes: Visualize electrical signals to analyze their waveform characteristics.
- Signal Generators: Produce electrical signals of various frequencies and shapes for testing.
- Spectrum Analyzers: Analyze the frequency spectrum of signals to identify component frequencies.
- Power Meters: Measure the electrical power consumption of devices and systems.
Calibration Frequency for Testing Equipment
Calibration is essential for ensuring accuracy in measurements. Guidelines for calibration frequency include:
- Annually: Most general-purpose electronic testing equipment should be calibrated at least once a year.
- Semi-Annually or Quarterly: Equipment used in critical applications or under extreme conditions may require more frequent calibration.
- After Repairs: Calibration should always be done after any repairs or adjustments to the equipment.
Industries That Rely on Electronic Testing Equipment
Several industries extensively use electronic testing equipment, including:
- Electronics Manufacturing: For quality control and testing of electronic components and assemblies.
- Telecommunications: To ensure signal integrity and equipment performance.
- Automotive: For testing electronic control units and vehicle systems during production and maintenance.
- Healthcare: In the calibration and maintenance of medical devices and diagnostic equipment.
- Aerospace: For rigorous testing of avionics and navigation systems prior to deployment.