PLC systems for industries
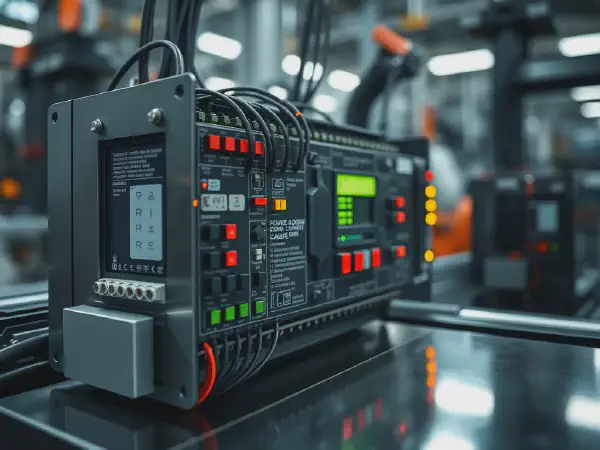
Plc Systems For Industries
Understanding PLC Systems
Definition of Programmable Logic Controllers (PLCs)
A Programmable Logic Controller (PLC) is a specialized industrial digital computer designed to control and monitor complex manufacturing processes and machinery. PLCs are robust and resilient, engineered to withstand harsh environments like extreme temperatures, electrical noise, and mechanical vibrations. They consist of a programmable microprocessor, input/output (I/O) modules, and communication interfaces, allowing them to handle various automation tasks with precision and reliability. Their programmable nature allows for easy adaptation to changes in the process without requiring significant hardware alterations, making them integral to modern industrial automation.
Historical Development of PLCs
The journey of PLCs began in the late 1960s, specifically within the automotive manufacturing sector, where they were developed to replace cumbersome relay logic systems that required extensive wiring and manual reconfiguration. The first-ever PLC, the Modicon 084, was introduced in 1968 by Bedford Associates, revolutionizing industrial control by offering flexibility and ease of programming. Over the decades, PLCs have evolved significantly, transitioning from simple relay emulators to complex control systems capable of integrating with advanced networking protocols and performing real-time automation tasks. Their ability to adapt to various applications has solidified their position as indispensable tools in industries ranging from manufacturing to pharmaceuticals, encapsulating a legacy of innovation in automation.
Understanding the Functionality of PLCs
Key Components and Architecture of a PLC
Programmable Logic Controllers (PLCs) are composed of several core components that work in tandem to manage and control industrial processes effectively. The primary elements include:
-
CPU Module: The brain of the PLC, the central processing unit (CPU) interprets inputs from sensors, executes the control program stored in memory, and triggers outputs based on that logic.
-
Power Supply Module: This module converts AC voltage to the necessary DC power required for the CPU and I/O modules, ensuring optimal performance and reliability.
-
Input/Output (I/O) Modules: I/O modules connect the PLC to external devices, acquiring data from sensors (inputs) and sending commands to actuators, motors, or alarms (outputs). These modules can handle both digital and analog signals to gauge various process conditions such as temperature and pressure.
-
Communications Interface: Enabling data exchange with other systems, the communication interface supports protocols like Modbus and Ethernet for effective connectivity with external devices and networks.
This architecture allows for robust performance in various industrial environments, ensuring PLCs can handle tasks ranging from simple relay operations to complex automation processes.
Programming Logic and Control
The operational backbone of a PLC is its programming logic, which dictates how inputs are interpreted and corresponding outputs are generated. PLCs typically use:
-
Ladder Logic: The most common programming language for PLCs, ladder logic resembles electrical relay diagrams, making it intuitive for engineers familiar with traditional control systems.
-
Structured Text: A high-level programming language that allows for more complex operations and conditions; it's akin to conventional programming languages like Pascal.
-
Function Block Diagrams: Graphical representations of functions, where various operations can be visually linked to show processing flows.
Programming a PLC requires specialized knowledge, yet user-friendly interfaces and simulation tools have made it more accessible for engineers without extensive programming backgrounds. This evolution allows for rapid adjustments in automation processes, thereby enhancing productivity and operational efficiency.
Input and Output Operations in PLCs
The Input/Output operations of PLCs are crucial for their function in industrial automation. These operations involve:
-
Input acquisition: PLCs gather data from multiple sources such as sensors and switches, translating physical conditions into actionable data.
-
Output control: After processing the inputs through the control program, PLCs generate outputs that actuate machinery, control lighting systems, or sound alarms, effectively managing the automation process.
-
Signal Type Handling: PLCs differentiate between discrete digital signals (on/off states) and analog signals (continuous values), enabling precise control over a wide variety of devices and processes.
These I/O operations ensure that PLCs not only react to changing conditions within industrial settings but also communicate results and status updates for effective monitoring and control. This integrative capability highlights the essential role of PLCs in maintaining operational efficiency across numerous applications.
PLC Systems for Industries | Features of PLC Systems | Applications of PLC Systems | Benefits of PLC Systems |
---|---|---|---|
Robust Industrial Control | Ruggedized design for harsh environments | Manufacturing automation, e.g., assembly lines | Flexibility in programming and reprogramming |
Digital Input/Output Handling | High reliability and ease of use | Power generation and distribution | Enhanced reliability and durability |
Modular Expansion Capabilities | Easily scalable with I/O modules | Chemical processing and batching | Real-time operation and control |
Easy Fault Diagnosis | Built-in diagnostics for troubleshooting | Water and wastewater management | Quick diagnostics and troubleshooting capabilities |
User-Friendly Programming | Ladder logic programming for ease of use | Food and beverage processing | Safety features for critical applications |
Types of Programmable Logic Controllers (PLCs)
Fixed, Integrated, and Compact PLCs
Fixed or Integrated PLCs, also known as compact PLCs, have their I/O modules integrated directly into the controller. This design limits expansion options, making them ideal for straightforward applications where input and output requirements are predetermined and do not require customization. The compact nature of these PLCs makes them suitable for smaller machines or processes that demand a reliable solution without the need for extensive I/O configurations. They are typically easier to install and maintain, offering a cost-effective solution for non-complex tasks in various industries.
Advantages of Fixed PLCs
- Simple installation and setup.
- Cost-effective for low to medium complexity applications.
- Reliable performance in stable operational environments.
Modular PLCs
Modular PLCs provide flexibility and adaptability by allowing users to add or replace individual I/O modules as needed. Each component, such as power supplies, communication interfaces, and I/O modules, is separate, enabling tailored configurations that can grow with the specific needs of an application. This design is particularly advantageous in complex systems that may evolve over time, allowing for expansion and modification without the necessity of replacing the entire system.
Benefits of Modular PLCs
- High customization potential with scalable I/O options.
- Easier maintenance, allowing for component replacement without system downtime.
- Suitable for complex operations requiring extensive monitoring and control capabilities.
Applications of Programmable Logic Controllers Across Industries
Automation in Manufacturing
In the manufacturing sector, Programmable Logic Controllers (PLCs) play a crucial role in automating production lines, which enhances both efficiency and accuracy. By controlling machinery and streamlining processes, PLCs ensure consistent quality in products, such as in the assembly of electronics or consumer goods. Their capability to adapt to various production processes contributes significantly to reducing downtime and waste, ultimately increasing profitability for manufacturers.
Power Generation and Distribution Systems
PLCs are integral for managing power generation and distribution. They monitor electrical distribution systems, balancing loads and controlling circuit breakers. For instance, PLCs facilitate the integration of renewable energy sources like solar and wind power into the existing grid. This management capability helps optimize energy distribution and improve the reliability of power supply.
Chemical and Petrochemical Processes
In the chemical and petrochemical industries, PLCs are essential for controlling intricate processes like mixing and chemical reactions. Their precision ensures that these processes comply with strict safety and quality standards, mitigating risks associated with hazardous materials. Furthermore, PLCs streamline batch processing operations, enhancing productivity and safety in chemical manufacturing.
Food and Beverage Control Systems
The food and beverage sector leverages PLCs to maintain high standards in production processes. They manage operations in food processing, bottling, and packaging, ensuring consistent product quality and adherence to health regulations. By precisely controlling temperatures and other processing conditions, PLCs help maintain food safety and compliance while boosting operational efficiency.
Streamlining Automotive Manufacturing
In the automotive industry, PLCs standardize production processes to maximize returns on investment (ROI). By automating repetitive tasks such as assembly line functions, PLCs not only minimize variability but also enhance both product quality and production output. Their reliability and flexibility make them invaluable in a sector where efficiency directly impacts competitiveness.
Pharmaceutical Industry Monitoring
The pharmaceutical sector relies heavily on PLCs for overseeing drug production processes. These controllers ensure precise ingredient mixing and stringent monitoring of environmental parameters throughout production. By maintaining high compliance with health regulations, PLCs play a vital role in safeguarding public health while optimizing production workflows.
Advantages of Programmable Logic Controller (PLC) Systems
Unmatched Flexibility and Reliability in Automation
Programmable Logic Controllers (PLCs) stand out for their remarkable flexibility in programming, enabling businesses to adapt to changes in production processes without necessitating hardware modifications. This adaptability is crucial in dynamic environments where operational requirements frequently shift. Additionally, PLCs are designed to function reliably in harsh industrial conditions, providing consistent performance despite extreme temperatures, vibrations, and electrical noise. By utilizing modular designs, PLC systems can be easily expanded with additional input and output (I/O) modules, ensuring scalability to meet evolving operational demands.
Real-time Control Capabilities
PLCs offer essential real-time operation features, allowing for instantaneous responses to input signals and process events. This capability is vital in critical applications, such as high-speed manufacturing or safety-focused systems, where delays can lead to significant complications. With a focus on accurately executing tasks in response to real-time data, PLCs enhance efficiency and performance across various automation sectors.
Advanced Diagnostics and Safety Mechanisms
Equipped with sophisticated diagnostics tools, PLCs enable operators to monitor system performance continuously and identify faults quickly. This proactive approach minimizes downtime and streamlines maintenance efforts. Furthermore, many PLCs incorporate safety features aimed at compliance with industry safety standards. These systems often include specialized programming languages and certified safety modules, ensuring reliable operation in safety-critical applications. By integrating such safety mechanisms, PLCs provide not only operational efficiency but also enhanced protection for equipment and personnel.
Future Trends in PLC Technology
Innovations in Communication Protocols
As industries demand real-time data exchange and more sophisticated interactions within interconnected systems, advancements in communication protocols are pivotal for the future of Programmable Logic Controllers (PLCs). Traditional protocols such as Modbus and Ethernet/IP are being enhanced to support higher data throughput and improved interoperability between devices.
The integration of wireless communication solutions is also on the rise, facilitating remote monitoring and control capabilities. This enables PLCs to communicate seamlessly with other automation elements including sensors, drives, and HMIs, ultimately optimizing the entire automation ecosystem. Additionally, the development of open-source protocols fosters innovation, allowing manufacturers and users to create and adapt these systems to meet specific needs.
These advancements are critical for industries such as pharmaceuticals and automotive, where real-time data availability can significantly reduce operational costs and improve safety protocols by allowing for swift adjustments and monitoring of processes from anywhere.
Embracing IoT and Smart Manufacturing Integration
The convergence of PLC technology with the Internet of Things (IoT) is ushering in a new era of smart manufacturing. As manufacturing processes evolve toward Industry 4.0, PLCs are being redesigned to incorporate IoT capabilities, enabling them to connect to cloud services for enhanced data analytics, and predictive maintenance.
This integration allows for comprehensive analytics to be performed on real-time operational data, which leads to improved decision-making and efficiency. Incorporating machine learning algorithms into PLCs can optimize operations based on historical data, predicting potential failures and scheduling maintenance before equipment breaks down—thus minimizing downtime.
Moreover, the compatibility of PLCs with smart devices creates opportunities for enhanced automation systems where machines can autonomously communicate, analyze trends, and adjust processes to improve productivity. As more industries adopt smart manufacturing practices, the role of PLCs will become increasingly critical, driving significant efficiency and sustainability improvements in manufacturing processes.
Frequently Asked Questions (FAQs)
What Industries Utilize PLC Systems?
PLCs are widely used in various industries, including manufacturing, automotive, pharmaceuticals, food processing, water treatment, and energy. Their ability to withstand harsh environments while effectively controlling machinery makes them integral to these sectors.
What Are the Primary Advantages of Using PLCs?
PLCs offer several key benefits, including flexibility in programming, high reliability in extreme conditions, real-time operational capabilities, and built-in diagnostics for troubleshooting. Additionally, they provide a cost-effective solution for automation processes.
How Do PLCs Differ from Traditional Computers?
PLCs are specifically designed for industrial environments with rugged construction. Unlike traditional computers, which are versatile but not optimized for specific tasks, PLCs focus on executing repeatable control tasks in real-time, offering greater reliability under harsh conditions.
Can PLCs Be Programmed Without Prior Coding Experience?
Yes, many PLCs utilize user-friendly programming languages such as Ladder Logic, which simplifies the programming process. This design enables users without extensive coding knowledge to effectively configure and operate PLC systems.
What Are the Types of PLC Programming Languages?
PLCs typically support a range of programming languages, including Ladder Logic, Structured Text, Function Block Diagrams, and Sequential Function Charts. These languages adhere to the IEC 61131-3 standard, allowing for versatile programming approaches.
How Do PLCs Communicate with Other Devices?
PLCs communicate with other devices through various interfaces such as USB, Ethernet, and serial connections (RS-232, RS-485). They utilize standard industrial communication protocols like Modbus and EtherNet/IP to enable seamless data exchange with external systems.