Top Insights into Industrial Electronic Equipment Trends
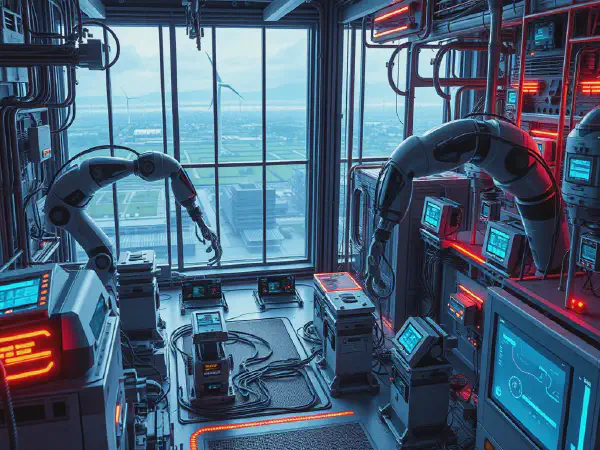
Understanding Industrial Electronic Equipment
Industrial Electronic Equipment refers to a variety of devices and systems utilized in industrial environments for the purpose of monitoring, controlling, and automating various processes. This category of equipment includes components such as sensors, actuators, controllers, and human-machine interfaces that work together to optimize industrial operations. Its integration into the manufacturing landscape has led to increased efficiency, reliability, and precision in processes that range from assembly lines to heavy machinery.
These systems are vital for improving not just productivity but also the quality of the products manufactured. Industrial Electronic Equipment is often connected to a central control system that allows for real-time monitoring and adjustments. This capability not only facilitates immediate response to any irregularities but also supports data collection for further analysis, aiding in long-term strategies for operational improvement and cost reduction.
Moreover, the diversity of Industrial Electronic Equipment enables it to be tailored to meet the specific needs of different sectors, including automotive, aerospace, pharmaceutical, and food processing. Each sector may require specialized equipment that adheres to industry-specific regulations and safety standards. As industries evolve, the functionalities of these devices continue to expand, incorporating advanced technologies that enhance their capabilities.
With a commitment to quality, esis pty ltd stands out in the competitive landscape of industrial electronics.
Due to the complex nature of industrial processes, the reliability of electronic equipment is paramount. Failures can lead to downtime, financial losses, and safety hazards. Therefore, periodic maintenance and upgrades are crucial to maintain optimal performance. As a result, companies are increasingly investing in robust Industrial Electronic Equipment to ensure operational excellence and competitive advantage.
Switching to a fanless pc can significantly reduce noise levels in your workspace, enhancing productivity.
In summary, Industrial Electronic Equipment constitutes the backbone of modern manufacturing and industrial processes. Its importance cannot be overstated as it plays a critical role in enhancing efficiency, safety, and product quality across various industries.
Discover how the innovative approach of esis is transforming local businesses in Thornleigh.
Applications of Industrial Electronic Equipment
Industrial Electronic Equipment finds a broad range of applications, one of the most significant being automation in manufacturing processes. This includes the use of programmable logic controllers (PLCs) and industrial computers to manage the tasks involved in production lines, thus reducing human error and optimizing workflow.
Energy management systems are another area where Industrial Electronic Equipment excels. These systems monitor energy usage and help in making real-time adjustments to reduce waste, leading to substantial cost savings and more sustainable operations. Such systems can integrate with renewable energy sources, promoting a more eco-friendly approach.
Process control is yet another critical application, where precise and continuous monitoring of industrial processes is required. This equipment ensures that production processes operate within predetermined parameters, thereby maintaining product quality and safety while minimizing environmental impact.
Industrial robotics and motion control greatly benefit from advanced Industrial Electronic Equipment. Robotics technology enables streamlined assembly, packaging, and inspection processes in manufacturing, enhancing flexibility and scalability and allowing businesses to respond swiftly to market demands.
Lastly, telecommunication equipment is essential in linking various components of industrial systems. Effective communication between different parts of the machinery and between machines and operators is crucial for seamless operations; this is facilitated by Industrial Electronic Equipment designed for telecommunication purposes.
Emerging Technologies in Industrial Electronics
The integration of IoT (Internet of Things) in industrial equipment signifies a revolutionary advancement in Industrial Electronics. IoT allows devices to remain connected and communicate with one another, leading to smarter decision-making based on real-time data. By harnessing IoT, industries can enhance operational efficiency and predictive maintenance.
Advancements in sensor technology are also opening new horizons for Industrial Electronic Equipment. Modern sensors are becoming more accurate, reliable, and capable of operating in harsh conditions. This progress enables more sophisticated data gathering and analytics, crucial for automation and process optimization.
Smart manufacturing and Industry 4.0 represent a significant shift in industrial practices. The focus on interconnected equipment, real-time data analysis, and adaptive manufacturing processes results in optimized production practices that reduce costs and improve quality.
Artificial intelligence (AI) in process optimization is emerging as a game-changer. AI algorithms can analyze vast amounts of operational data to predict failures, optimize maintenance schedules, and improve overall equipment effectiveness, making processes not only efficient but also cost-effective.
Wireless communication technologies are further enhancing the capabilities of Industrial Electronic Equipment, enabling remote monitoring and control. These technologies reduce cabling costs and increase flexibility in machine placement and operation, thus enhancing overall productivity.
Safety Standards for Industrial Electronic Equipment
Understanding IEC (International Electrotechnical Commission) and ISO (International Organization for Standardization) safety standards is vital for the effective utilization of Industrial Electronic Equipment. These standards lay out best practices and protocols that help ensure equipment safety and efficacy, establishing a framework that manufacturers must adhere to.
Risk assessment methodologies are key components of ensuring safety in industrial settings. These methodologies help identify potential hazards associated with the use of industrial equipment, allowing companies to implement controls and preventive measures to mitigate risks.
Compliance with electrical safety norms is essential to protect both personnel and equipment. Regular inspections and adherence to safety codes prevent accidents and ensure that the equipment operates within safe parameters, thus maintaining regulatory compliance.
Workplace safety in manufacturing environments cannot be overlooked, as proper training and usage of Industrial Electronic Equipment minimize the risk of accidents and injuries. Organizations must commit to continuous safety training and promote a safety-first culture among their workforce.
Finally, protective measures for personnel and equipment, including the use of safety guards, emergency shutoff systems, and proper personal protective equipment (PPE), are critical to maintaining safety standards in industrial environments. The implementation of these measures reflects a commitment to safeguarding not only the equipment but also the lives of those who operate it.
Market Trends and Projections
The growth forecast for industrial electronics remains optimistic, driven by increased demand for automation and connected systems across various sectors. Analysts predict a significant compound annual growth rate (CAGR) as more industries adopt advanced electronic solutions for greater efficiency.
Major players in the industrial equipment market include leading manufacturers and technology companies that continuously innovate and expand their offerings. These key players drive competition and technological advancements through research and development activities, leading to the rollout of more sophisticated Industrial Electronic Equipment.
The impact of globalization on manufacturing cannot be underestimated, as it has led to more interconnected markets and supply chains. As production processes become global, the need for advanced Industrial Electronic Equipment that can communicate and operate across diverse manufacturing sites becomes crucial.
Trends in sustainable industrial practices are emerging as critical drivers for the adoption of Industrial Electronic Equipment. Companies are increasingly focusing on energy-efficient systems and sustainable manufacturing processes to minimize their environmental impact and comply with regulatory requirements.
Investment opportunities in new technologies, particularly in automation and digitalization, are becoming increasingly prevalent as industries seek to modernize and enhance productivity. Investors are keen to support innovative solutions that enhance the efficiency and sustainability of industrial processes.
Maintenance and Reliability of Industrial Equipment
Predictive maintenance techniques are becoming essential for ensuring the reliability of Industrial Electronic Equipment. By leveraging data analytics and monitoring technologies, companies can identify potential issues before they lead to equipment failure, thereby reducing downtime and maintenance costs.
Lifecycle management of equipment extends beyond initial purchase, involving the planning, acquisition, utilization, and eventual disposal of equipment. Effective lifecycle management ensures that equipment operates effectively throughout its lifespan and minimizes the total cost of ownership.
The importance of calibration and testing can never be overstated; these practices are essential for ensuring that Industrial Electronic Equipment operates accurately and reliably. Regular calibration checks help maintain performance standards and ensure compliance with safety regulations.
Troubleshooting common electronic equipment issues is critical for maintaining operational continuity. Operators must be trained to diagnose and resolve minor issues quickly; this reduces downtime and enables smoother operations.
Finally, training and skills development for operators are vital components of maintaining reliable Industrial Electronic Equipment. As technology evolves, continuous training ensures that personnel remain competent and capable of operating equipment safely and efficiently.